A warehouse workstation is only as strong as its layout and design. Before maximizing efficiency, productivity, or flow, you have to find an organizing strategy that works for your team. With over 40 years of experience, we know what makes a robust and successful workstation, and we also know what the most common challenges in designing one are.
We've outlined The Top 10 Challenges in Designing a Successful Work Area as a resource for businesses looking to improve their current setup. Consider these common challenges as critical areas to consider as you develop your work area.
2. Inadequate Packaging Supplies: Insufficient packaging supplies can impede the packing process and lead to significant delays. To prevent bottlenecks and interruptions, businesses must ensure an adequate supply of packaging materials, such as boxes, tape, bubble wrap, and void fill. Regular inventory management and proactive supply chain planning can help alleviate this problem.
3. Insufficient Staffing and Training: Give your team the tools and resources they need to succeed. The efficiency of packing workstations relies heavily on skilled and trained personnel. Companies often face challenges in finding and retaining competent packers. Insufficient staffing can lead to delays, errors, and compromised quality. Providing comprehensive training programs, fostering a positive work environment, and implementing appropriate incentive structures can mitigate this issue. Invest in your employee's success, and you'll see an incredible difference in your business' output, morale, and efficiency.
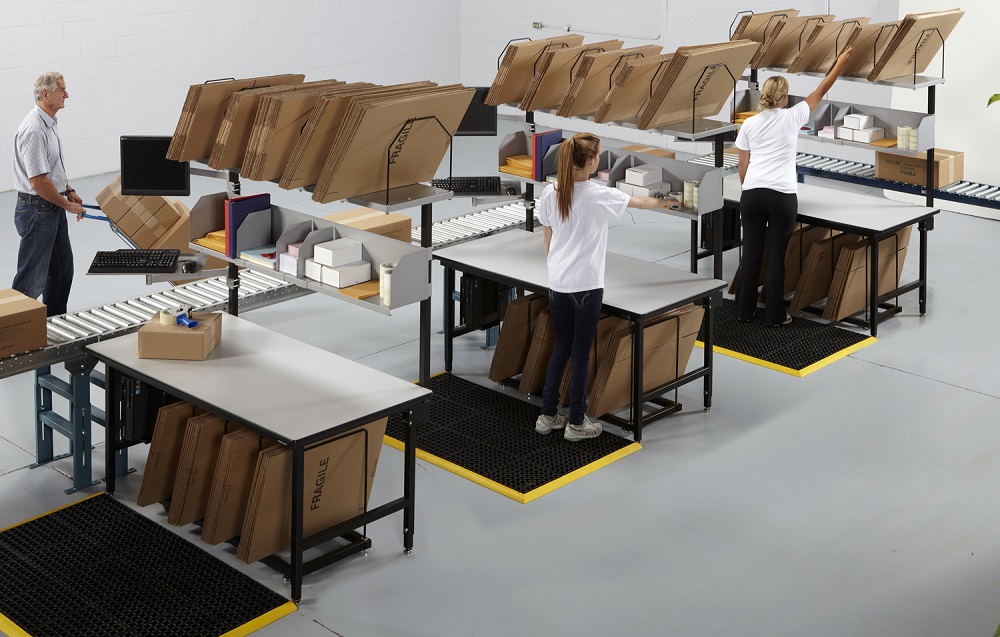
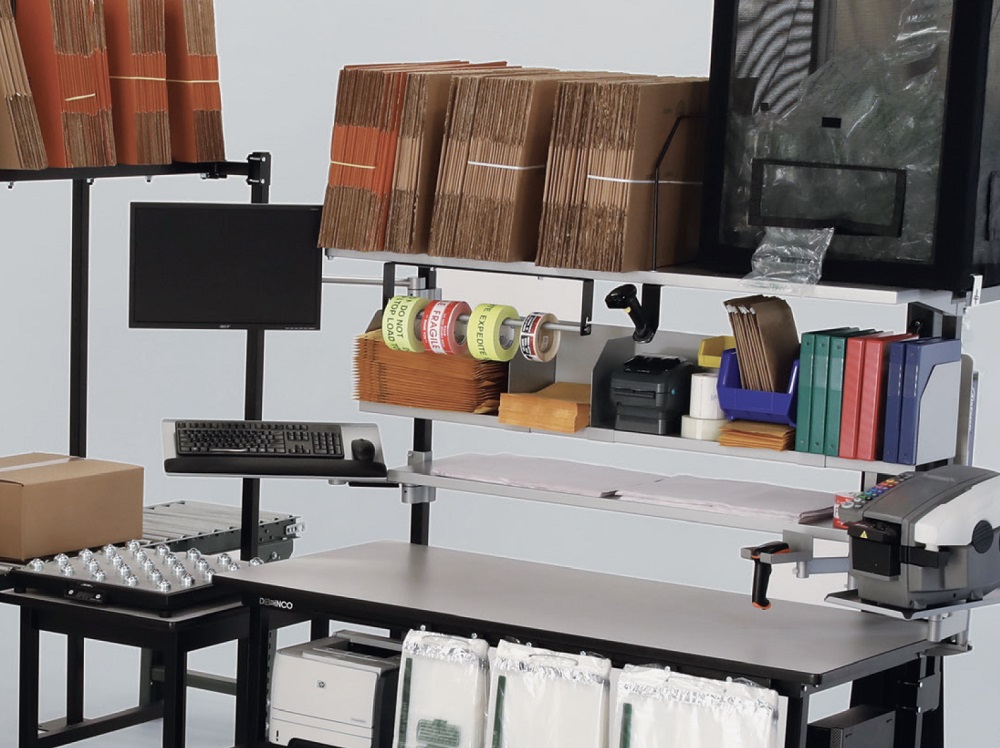
5. Ergonomics and Worker Safety: It's essential to set your team up so they can do their best work safely and competently. Poor workstation ergonomics can lead to employee discomfort, fatigue, and injuries. Companies should prioritize the design and setup of workstations to ensure ergonomically correct postures, easy access to supplies, and appropriate lifting and handling techniques. Regular ergonomic assessments and adjustments can promote worker safety and productivity.
6. Technological Integration: Technology and physical tasks should work hand in hand, each making the job easier every step of the way. Companies that fail to integrate technology into their packing workstations may encounter operational inefficiencies. Leveraging barcode scanners, automated packing systems, and warehouse management software can streamline processes, reduce errors, and enhance overall productivity. Investment in suitable technology and its seamless integration is essential for optimizing packing operations.
7. Order Complexity and Variation: Complex and diverse order requirements can pose a challenge for packing workstations. Companies may face difficulties handling orders with multiple items, different sizes, or specific packing instructions. Implementing advanced order management systems, utilizing customizable packing stations, and providing detailed order information to packers can aid in addressing this challenge.
8. Ineffective Communication and Coordination: Poor communication and coordination among different departments can disrupt the packing workflow. Businesses should establish effective communication channels, such as real-time messaging systems or intercoms, to facilitate clear instructions, resolve issues promptly, and coordinate tasks seamlessly. Regular team meetings and cross-departmental collaborations can enhance overall efficiency.
9. Quality Control and Inspection: Maintaining quality control and inspection standards during packing is essential to prevent errors, damages, and customer dissatisfaction. Implementing stringent quality checks, providing regular training on quality standards, and conducting periodic audits can ensure that packed orders meet the required quality criteria.
10. Continuous Improvement and Adaptability: We all work better when we work together. Businesses must embrace a culture of continuous improvement and adaptability to overcome evolving challenges in packing workstations. Regularly evaluating and optimizing processes, seeking employee feedback, and staying updated with industry best practices can help companies remain agile and responsive to changing demands.
Conclusion:
At Dehnco, we've designed our entire solutions suite to help you navigate and address these common warehouse challenges. For more information and inspiration for your space, visit our Solutions Concepts Library ( https://www.dehnco.com/solutions-design/solution-concepts-library/).